Turners (Soham) Ltd is one of the largest independently owned transport and cold storage companies in the country. Turners has expanded continuously since the company was established in 1930 and now operates 17 depots including one in the Netherlands.
Turner’s recently extended their distribution centre at Soham near Newmarket, Cambridgeshire, with the addition of a new cold storage building. Driftwood Construction Ltd was the main contractor with Twintec Industrial Flooring contracted to lay the floor inside the building.
For this job, Twintec opted to use a Camfaud 52 metre concrete boom pump for its reach and flexibility. The concrete floor design for the cold store called for the use of steel fibre reinforced concrete. This concrete is now the norm for cold stores and is also used for seamless floors and industrial floors supported by piled foundations.
Cemex delivered the base mix to site and Twintec dosed the mix with the correct amount of steel fibres. The dosing was carried out using a purpose built dosing device to ensure that the fibres were evenly distributed throughout the load.
Without this assurance, the material would not pump in a satisfactory way and might not meet the design parameters.
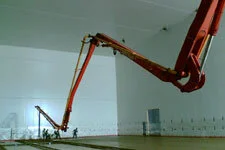
The Putzmeister M52 boom pump was chosen due to its reach, unfolding height and output. The height of the building was 15 metres which allowed easy manoeuvrability for the pump which requires a minimum unfolding height of 10.4 m.
The 48.1 m. reach ensured that the pour could be carried out “off the boom” rather than using ground line making the job, quicker, easier and safer. This pump has an output of up to 160 cubic metres of concrete per hour. However, as with most concrete pump jobs, the output achieved is determined more by the concrete supply and the ability of the gang to place the concrete than the capacity of the pump. The fibre dosing machine is used to separate the fibres and then convey them pneumatically into the drum of the truck mixer.
Experience has shown that this is the most efficient way of ensuring that the fibres are evenly spread throughout the mix. The machine can also dose a superplasticiser which, if used, is batched prior to the addition of the fibres.
The ready mix truck is required to mix the load for a further five minutes after the addition of the admixture and fibres to ensure a homogeneous mix is achieved.
-
Pump: M52
-
Customer: Twintec Industrial Flooring
-
Site: Turners (Soham) Ltd, Cold Store
-
Concrete Supplier: Cemex
-
Date: November 2005